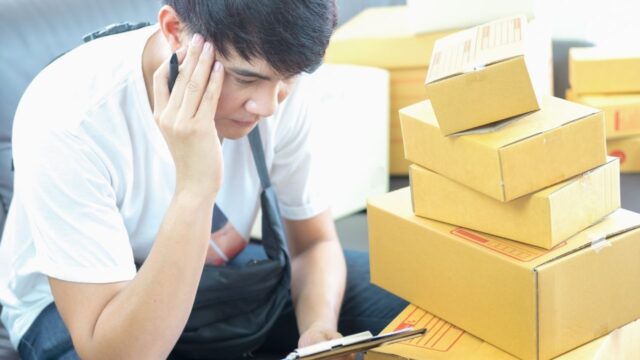
What is average inventory and why is it important
Average inventory is a measure of the average amount of inventory that a company has on hand over a period of time. The average inventory can be calculated by taking the total value of all inventory items and divided it by the number of days in the period. The average inventory helps businesses keep track of their stock levels and ensure that they have enough inventory on hand to meet customer demand. It also helps businesses manage their working capital, as too much inventory can tie up cash that could be used for other purposes.
In addition, the average inventory can be a valuable tool for forecasting future sales and demand trends. By understanding how much inventory is on hand, businesses can better plan their production schedules and make sure that they have the necessary products and materials on hand to meet customer needs. As a result, the average inventory plays an important role in helping businesses operate effectively and efficiently.
How to calculate average inventory
Inventory is a key piece of information for any business owner, and calculating the average inventory can give you a valuable insight into your company’s health. There are a few different ways to calculate average inventory, but the most common method is to use the weighted average formula. This formula takes into account the number of units of each item in inventory as well as the cost of each unit. To calculate the weighted average, simply multiply the number of units of each item by its cost, and then add all of these numbers together. The result will be your average inventory cost. This number can be useful in determining your company’s overall profitability as well as in making decisions about pricing and production levels.
Factors that can affect average inventory
There are a number of factors that can affect average inventory levels. One is the amount of turnover, or how quickly inventory is moving. A high turnover rate will result in lower average inventory levels, while a low turnover rate will cause levels to rise. Another factor is the Mix of products being sold. A product mix with a large number of SKUs will generally have higher inventory levels than one with fewer SKUs.
Finally, the order frequency can also impact average inventory levels. Higher order frequency means that items are replenished more often, resulting in lower average inventory levels. Conversely, lower order frequency leads to higher inventory levels. By understanding these factors, businesses can better manage their inventory and ensure that they have the right level of stock on hand at all times.
Uses of average inventory data
Businesses use inventory data to track their stock of goods. This information is used to make strategic decisions about production, purchases, and sales. Inventory data can also be used to assess the effectiveness of current inventory management practices. For example, if a business notices that its inventory turnover rate is low, it may decide to implement changes to its production or purchasing procedures.
Additionally, businesses can use average inventory data to forecast future demand. This information can be helpful in planning for seasonal fluctuations in demand or unexpected changes in the market. By understanding how inventory levels fluctuate over time, businesses can ensure that they have the right amount of stock on hand to meet customer needs.
Methods for reducing average inventory levels
There are a number of methods businesses can use to reduce their average inventory levels. One common method is to increase the frequency of inventory turnover. This can be done by reducing the time it takes to receive new shipments, increasing sales, or both. Another method is to employing just-in-time production, which minimizes the amount of inventory on hand by only producing goods as they are needed.
Finally, businesses can also reduce waste and spoilage by improving their storage and handling procedures. By taking these steps, businesses can effectively reduce their inventory levels and improve their bottom line.
Why average inventory is critical for businesses of all sizes
Assuming that a business sells products that have a shelf life, it is important to track inventory levels so that shelves are not emptied and customers are not left waiting. This becomes increasingly critical as businesses grow in size and scale. An average inventory level lets businesses know how much product they need on hand at any given time in order to meet customer demand. This information is essential for determining both production schedules and pricing. Too much inventorytie up valuable resources, while too littleinventory can lead to lost sales. As a result, maintaining an accurate average inventory level is crucial for businesses of all sizes.
3 steps to take if your business is struggling with high inventory levels
Maintaining healthy inventory levels is a vital part of successful business management. Having too much inventory can tie up valuable resources and lead to storage problems, while having too little inventory can result in lost sales and unhappy customers. If your business is struggling with high inventory levels, there are a few steps you can take to correct the problem.
First, take a close look at your sales data to identify slow-moving items. These are the items that are taking up valuable space in your warehouse but aren’t selling very well. You may want to consider discontinuing these products or reducing your order quantities for future orders.
Second, take advantage of special promotions or discounts offered by suppliers to help clear out excess inventory. And finally, consider implementing just-in-time ordering for key items to help ensure you don’t have too much inventory on hand at any given time. By taking these steps, you can help bring your inventory levels back into balance and keep your business running smoothly.