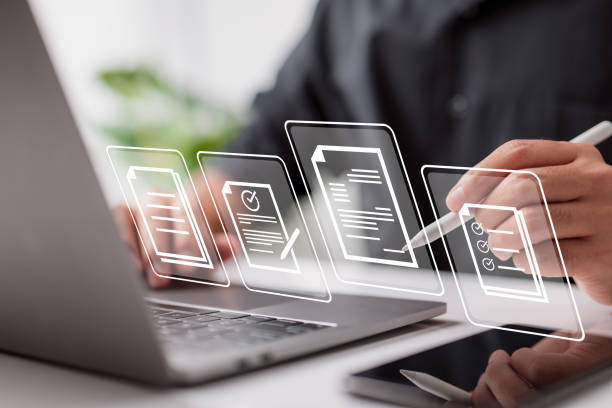
In manufacturing, automation is vital to maintaining high-quality standards — ensuring products meet compliance requirements and are defect-free. Those who embrace workflow automation, primarily through Quality Management Software (QMS), can benefit significantly. They can foster better communication and reduce process errors. Ultimately, this allows them to stand out in a crowded marketplace by consistently delivering quality products to their customers.
The Need for Automation in Modern Manufacturing
Today’s customers demand quality products that are delivered quickly. This requires manufacturers to adopt systems that can efficiently mass produce, package, and distribute inventory while minimizing defects and meeting compliance standards. Automation isn’t just a nice-to-have technology anymore. It’s necessary to keep manufacturing operations running efficiently and reduce process errors so that customers can get what they need when needed.
Automation enhances efficiency by putting repetitive processes on auto-pilot, like inventory management, production scheduling, invoicing, and quality control. In quality management, automated systems offer significant advantages. Instead of manually checking each unit for defects or compliance, these systems can monitor production processes and inventory. This approach not only saves time but also reduces the likelihood of errors.
Key Features of Automated EQMS in Manufacturing
The best way to automate your manufacturing plant is through Enterprise Quality Management Software (EQMS). This software improves both the speed and quality of product production. Some of the key automation features for EQMS software include:
- Automated production monitoring: Real-time tracking and data collection of production processes with automated alerts and dashboard analytics to spot issues that could result in product defects or process inefficiencies.
- Predictive maintenance: Monitoring systems that identify impending equipment failures based on conditions, predictive analytics, and routine maintenance schedules before impacting the production line or quality control.
- Process optimization: Data analysis features that automatically spot bottlenecks and improvement opportunities in production or inventory management processes for swift, effective remediation.
- Change or recall deployment: Auto-requesting or approving changes from the top-down, such as product recalls, new materials, or new processes, that get communicated, administered, and tracked for implementation progress.
- Communications and data synchronization: Systems that automatically share reports, provide updates, assign tasks, or make change requests to different teams outside of operations. It also includes using integrations that automatically update data records in other systems, such as customer relationship management (CRM), enterprise resource planning (ERP), or supply chain management software.
For manufacturers, a robust automated EQMS platform provides real-time data insights on production lines and inventory and streamlined communications. Leveraging such automation ensures you can find process issues and implement value-added changes to the operation without downtime.
Benefits of Integrating Quality Software with Automation
Integrating an automated QMS in your manufacturing processes is a game changer for enhancing your operations and customer relationships. Some of the primary benefits include:
- Improved quality control processes reduce the likelihood of defects. Achieve this by taking error-prone, manual processes out of the equation while inspecting products and production workflows.
- Reduces waste of manufacturing materials, labor, and other resources by proactively spotting process issues and impending defects and fixing them before they impact your bottom line.
- Optimal allocation of resources by tracking production processes and inventory for bottlenecks automatically, then quickly administering changes such as a new process, equipment, or materials without wasting time or shutting down the production line.
- Better cross-functional communications by letting the operations team automatically share data insights or assign tasks to other teams, like billing, sales, or logistics.
The overall result of making a digital transformation by adopting an automated QMS software in manufacturing is operational excellence. Your production lines can run more efficiently using fewer resources and ensure quality products are delivered to customers. This leads to higher retention, sales, and a boost in profitability.
Implementing Automated EQMS in Manufacturing
Implementing EQMS to help automate your manufacturing operation and quality control is no easy feat. Many companies operate out of older facilities, utilizing highly tailored operational technology (OT) to meet their production needs. This often leads to system compatibility issues between a desired QMS software and the monolithic IT stack, particularly during installation and integration with other tools.
There’s also the question of scalability. You need to find a platform that can accommodate changes to your business needs. It should automatically process and analyze vast amounts of production line data without slowing down. Additionally, the platform must quickly adapt to rapidly changing customer demands, especially during busy seasons that require increased production output.
Finally, there’s the human side to implementing automation software. For high user adoption rates and to maximize your EQMS investment, you must plan to provide robust training. This training should focus on operating the system, creating workflows, and interpreting prescriptive analytics, among other aspects. Continuously highlight the benefits of deploying automation throughout your manufacturing facility. Doing so will excite your personnel about the new system.
Overcoming Challenges in EQMS Automation
While the benefits of EQMS automation in a manufacturing facility are invaluable, there are some early roadblocks you’ll need to overcome.
Technological adaptation is the first to address. As mentioned, many manufacturers operate using outdated facilities, making it challenging to transform digitally. They often rely on clunky OT systems and custom ERPs and CRMs, which are not integration-friendly, instead of using convenient cloud-based applications. Your EQMS adoption journey must start with a compatibility evaluation with existing systems and a development plan to prepare your tech stack for the new software.
Cost is another challenge that deters manufacturers from evolving into automated machines. Between the costs of the EQMS platform, implementation, and provider support, it can eat at your bottom line. Overcome this by focusing on the benefits and potential ROI yet to come as a selling point for top-down support. You can also segment implementation by prioritizing specific processes. For instance, adopt predictive maintenance and slowly add automation to other areas over time.
Ready to Move Your Manufacturing Facility Towards Automation? ETQ Can Help.
Automation through QMS software is vital for manufacturers to streamline quality control across their product life cycles, minimize defects, and maintain compliance. You can achieve operational excellence and boost customer satisfaction by adopting an EQMS that meets your specific tech stack and scalability requirements. This will give your business a distinct competitive advantage through automation.
ETQ empowers manufacturers to increase product quality while decreasing operational inefficiencies and costs through our quality management solutions.
Contact us today to see how we can help you harmonize quality management across your entire product lifecycle and at every manufacturing facility through QMS software.