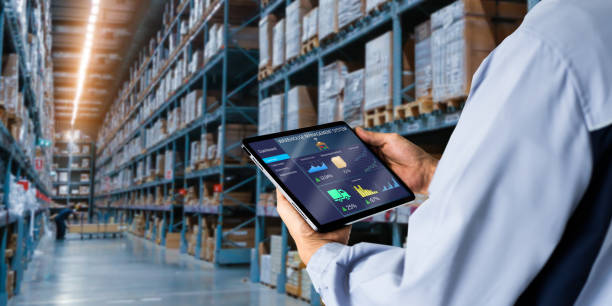
Logistics is one of the most essential parts of your business; how it runs is vital to your success. This is the overall process of managing your resources for acquisition, storage, transportation and final delivery. Often, issues along the line stop the flow of goods.
Problems do arise from manufacturers to distributors and suppliers to trucking companies. However, how you handle them determines the net effect of issues in the supply chain.
There are solutions to common logistics problems. Whether you handle some, all, or none of your logistics operations, it is essential to recognize and correct issues. This is so your business runs smoother, and your customers are happy and ready to order in the future.
Here are five solutions for common problems in the logistics industry.
Rising Fuel Costs
Rising fuel costs impact every sector, but transportation’s effects are most evident. As diesel and gasoline prices climb, it creates a chain reaction that ultimately shrinks your profit margins.
Using route optimization tools, you can find shorter paths that make deliveries more efficient. Training your drivers ensures they clearly understand their destinations, which prevents unnecessary detours. Another practical approach is fuel-efficient vehicles, such as hybrids and electric cars.
It’s also wise to minimize idleness whenever possible since it can consume up to half a gallon of fuel per hour. In some cases, outsourcing your deliveries to a freight forwarder that specializes in bulk shipping might be a savvy move to reduce costs.
By adopting these measures, you can manage fuel expenses more effectively. Keeping these costs under control is crucial for maintaining your profits and customer satisfaction.
Using a Third Party Logistics Company
It can be overwhelming and time-consuming for those who manage their fulfillment and supply chain. There comes a point where your business is better served by outsourcing some or all of the logistics operations. This is so you and your staff can concentrate on the core components of your operation.
A third party logistics company, often called 3PLs, focuses on client service rather than product sales. They have established a vast infrastructure designed to address your evolving logistical needs. They manage all logistics stages to ensure seamless operations.
The process begins with procurement. These companies place and receive orders from your wholesalers and suppliers. At the storage stage, your inventory is securely housed in their facilities across various global locations.
Regarding order fulfillment, they receive orders from your customers and ensure items are picked and packed efficiently for prompt delivery. Transportation is also handled adeptly. They utilize a large fleet of delivery vehicles and have partnerships to enable local and global shipping of your products.
Returns are processed carefully. Items shipped back to them are handled diligently, with refunds processed at your request or automatically. This is to ensure customer satisfaction and the smooth operation of the return system. By using a 3PL company, your logistics problems will go away.
Our distribution centers and warehouses can be busy with supplies, inventory turnover, and products picked, packaged and shipped. While you try to run it smoothly, errors still occur, and this can cause major problems like:
- Running out of stock
- Expired products
- Shipping wrong items
- Incomplete orders
- Wrong shipping address
Usually, it comes down to human error. However, this can be avoided by implementing new technologies like automated picking and packing systems, AI automation and other management systems into your operation. These check the process and streamline your operation while reducing errors.
Communication
A large part of the breakdown in your logistics operation is due to a lack of communication. Maintaining regular communication with all your partners is key to efficiently moving goods in your supply chain. This is also key to the successful delivery to the end customer.
Create a team to handle this for you. Experienced IT support can use real-time communication to keep in touch with vendors and delivery personnel during backups or emergencies, allowing rapid solutions to be implemented. Regular communication with suppliers ensures you are current with your products and strengthens your supply chain.
Ensure you constantly communicate with your warehouse and transportation companies to ensure your goods move efficiently.
Employee Management
Your employees are the lifeblood of your business, and they make your logistics run smoothly. Not only do you need the right people for the job, but there must be effective leadership and systems to manage them efficiently. Different teams will strive to work in sync, which can be difficult if everyone is not on the same page.
Introduce training so each team member knows their job and consider cross-training and moving staff around periodically. This helps when you are understaffed and engages your workforce more in the business. Also, have well-defined processes that everyone can follow without confusion.
Make sure to put employees in roles they can thrive in. Look for talented people who can rise and take on more complicated tasks. When you manage your team effectively, you can overcome many logistics challenges.