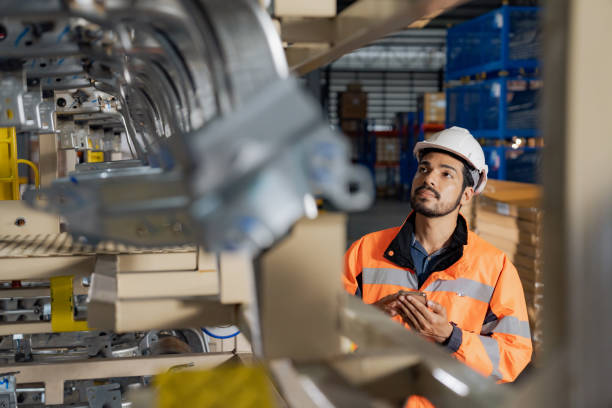
Industrial and manufacturing sectors are in constant evolution. The transformation includes countless improvements, such as technology integration, process refinement, automation, software solutions, and data-driven decisions. However, the change should be guided and well-thought-out. This article provides essential tips to help you holistically and effectively improve your manufacturing plant. Keep reading to learn more.
The Importance of Regular Equipment Maintenance
One of the key components of an efficient manufacturing plant is the state and performance of its machinery. Regular maintenance should be a priority. Manufacturers often lose significant amounts of money due to equipment failure and the resulting downtime. Adopting a proactive approach instead of a reactive one is essential, as diagnosing issues early can help avoid costly repairs and unplanned downtime.
Investing in predictive maintenance is a smart move for businesses looking to optimize their operations and reduce downtime. This innovative approach utilizes sensors, artificial intelligence, and data analysis to monitor the condition of machines and predict when they are likely to fail. By understanding the patterns and trends in machine behavior, predictive maintenance can alert maintenance teams to potential issues before they lead to costly breakdowns.
The use of sensors allows businesses to collect real-time data on the performance and condition of their equipment, providing valuable insights into any potential faults or wear and tear. This data is then fed into advanced artificial intelligence algorithms, which analyze the information and identify patterns that precede equipment failure. By detecting early warning signs, businesses can take preventive action, conducting maintenance or repairs before a breakdown occurs.
Not only does predictive maintenance help to avoid unexpected breakdowns, but it also contributes to the overall longevity of the equipment. Regular maintenance, as recommended by predictive maintenance systems, helps identify and rectify small issues before they escalate into major problems. By addressing these smaller issues promptly, the lifespan of the equipment can be significantly extended. This saves businesses money long-term by reducing the need for major repairs or premature replacements.
However, to make the process of predictive maintenance even more efficient and effective, it’s essential to invest in cost, price, quote (CPQ) software. CPQ software solutions streamline the sales process by allowing sales teams to accurately configure, price, and quote products. When it comes to preventive maintenance, CPQ software can play a significant role in scheduling and conducting maintenance tasks efficiently, ensuring that all necessary maintenance updates are completed on time.
Implementing Lean Manufacturing Techniques
Lean manufacturing is a systematic method for waste minimization within a manufacturing system without sacrificing productivity. It can play a significant role in enhancing production efficiency and reducing waste. Lean principles aim to create more value for customers by optimizing the flow of products and eliminating waste practices.
It’s not only about being more efficient on the production line. Lean manufacturing uses less energy, reduces waste, and improves productivity simultaneously. By observing lean principles, you can enhance your profitability while boosting customer satisfaction with your products.
Adopting lean techniques in your manufacturing processes means systematically seeking out inefficiencies in your production process and eliminating them. This ongoing process of locating and removing waste through lean manufacturing principles can significantly improve the performance of your manufacturing plant.
Boosting Employee Morale and Training
Employees who are dissatisfied or untrained can lead your manufacturing plant to less efficiency, more errors, and higher turnover rates. For this reason, boosting employee morale and providing adequate training is essential. With a proper system, you can boost productivity and handle minor issues before they become major problems.
Training your employees not only equips them with needed professional or technical skills but also shows them that you are investing in them, which boosts morale. Emphasize creating a work environment where employees feel valued and part of a team. Equip your team with the necessary tools and knowledge to increase their performance. When employees get comfortable in their roles, they are bound to perform better, which means higher quality output for the company.
Training programs also help retain staff, as well-trained and content employees are less likely to leave, reducing the costs of hiring and training new staff. Additionally, employees who receive training to update their skills will bring ideas to innovate and streamline production processes.
Embracing Advanced Technologies
The introduction of advanced technologies is revolutionizing manufacturing plants. Technology is the future of manufacturing, from autonomous robots that work side by side with humans to predictive maintenance sensors. Implementing these technologies can significantly boost productivity, reduce costs, and improve accuracy.
The Fourth Industrial Revolution, known as Industry 4.0, fundamentally changes how businesses operate and work. Technologies like the Internet of Things (IoT), artificial intelligence (AI), and cloud computing lead this change. Embracing these technologies can result in improved productivity and revenue.
These advanced technologies offer a competitive advantage to those businesses that choose to embrace them. The sooner these technologies are adopted, the quicker businesses can reap the benefits of their investments.
Promoting a Culture of Quality
Promoting a culture of quality within your company can have numerous benefits. A quality culture is one where the goal of customer satisfaction via product or service excellence is paramount. Everybody in the organization understands their role in achieving this goal, and they each perform their duties to the best of their abilities.
In a culture of quality, employees are encouraged to take ownership and responsibility for the tasks they perform. This not only improves efficiency but also reduces the chance for errors or mistakes to occur.
Quality should not be the sole responsibility of one department or a team but should permeate all levels of the organization. This includes management, shop floor employees, and even supply chain partners. Ultimately, this helps improve the plant’s overall performance and increases customer satisfaction.
Sound Inventory Management
Inventory management can make or break a manufacturing operation. Therefore, a solid inventory management system is key to running your manufacturing plant at peak performance. With an effective inventory management system, you can plan and control your inventory to ensure you always have the right stock levels.
A streamlined inventory management system will keep your costs down, reduce the amount of capital in inventory, enhance cash flows, and boost your profitability. Inventory management is not just about storing and counting goods. It’s about understanding the dynamics of your business so that every decision brings you one step closer to your profit goals.
Many inventory management software solutions are available that can help automate the process, making it more efficient and accurate. They help track inventory levels in real time, forecast demand, reduce waste, and improve customer service.
Improving Supplier Relationships
Your suppliers provide the materials and services you need to run your manufacturing plant. Having a good relationship with them can affect every aspect of your operations. When manufacturers provide suppliers with their future production plans as part of their business practices, this can result in cost savings due to increased production efficiencies and less waste.
Strong supplier relationships can also result in additional business opportunities. Suppliers may be willing to monetary or physical resource pool, offering innovations that can improve product processes to help the companies they do business with succeed.
Respect and communication are the keys to a successful relationship with your suppliers. Companies that cultivate good, strong relationships with their suppliers often receive better service and have access to help when needed. This ultimately enhances the efficiency of the plant.
Improving your manufacturing plant involves a combination of solutions. A well-organized and efficient manufacturing plant not only increases productivity but also reduces waste and the cost of production.